News
Leadership in a time of crisis: lessons for the AfCFTA
Africa needs to do more internally. Developing a regional value chain will comprise bigger industries obtaining their supplies from smaller industries across Africa's borders.
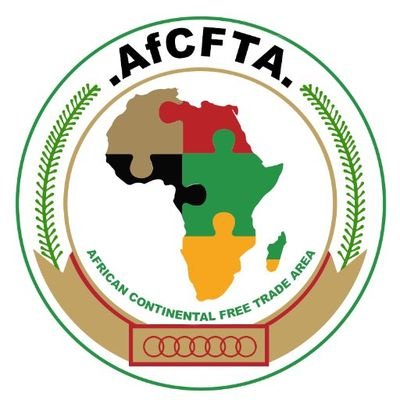
Tyrone Avenue is the picturesque main street of Parkview, Johannesburg. Normally home to strolling families, tourists and seekers of a tranquil shopping experience, it is much quieter today. It was this way last week too. A local supermarket here has half its shelves emptied and employees encourage you to look elsewhere for toiletries and other essentials. A lot is changing.
The start of the coronavirus pandemic in China in December last year is the newest in a succession of diseases — SARS, Ebola, swine flu, avian flu — that have somehow migrated from animals to the human population. Before the outbreak, global growth was pegged at 2.3% but according to the Economist Intelligence Unit, this is now likely to only be 1.9% — the slowest growth rate since the global financial crisis. Estimated loss of global real GDP is an estimated $2.3-trillion.
The African Development Bank’s 2020 African Economic Outlook projected 3.9% growth for the continent in 2020, and 4.1% in 2021 — confirmation of the continent’s rise as a destination for growth and investment. Today, due to the onslaught of COVID-19 and other factors, such as the declining oil prices and large swathes of locusts devastating agricultural fields, the UN Economic Commission for Africa’s recent projections for 2020 shows Africa will likely have 1.8% growth, with its oil-exporting countries Nigeria, Angola, Gabon, the Democratic Republic of the Congo (DRC) and Algeria, hardest hit.
Additionally, the continent is expected to see in excess of $10bn in unanticipated health spending and fiscal stimulus packages and, regrettably, depending on the duration and severity of COVID-19, the costs could be larger. If ever there was a time for strong leadership, it is now, and Africa must rise to the challenge.
Thankfully, one thing that has emerged from this crisis is a refocus on what really matters: people. The human race, advanced as it may be, has been put to the test by an invisible, biological threat.
The solution has so far been social isolation, social-distancing and locking down whole cities and countries — a temporary measure that may change the way people conduct business for some time to come. Most importantly, the world has had to come to terms with a key vulnerability in global trade: the dominance of China, and the Far East, as the global manufacturing hub.
The origins of the current supply-chain predicament arise from decisions to rely on one supplier or one region for various cost and sometimes property rights reasons. Such decisions cascade down through supply chains, even influencing those businesses that do not directly source materials or products from China themselves, but whose suppliers do.
Many multinationals learnt this lesson with the March 2011 earthquake in Japan, but it seems much of it got lost over the years. Now, COVID-19, with a much broader reach, has exposed these vulnerabilities and perhaps will awaken global operations’ management procedures.
China's grinding halt
The Chinese economy is suffering a historic slump as much of the nation’s economic activity came to a grinding halt. Retail sales nose-dived 20.5% by end of February, in comparison to a projected 4% decline. Unemployment was no exception as millions lost their jobs and unemployment rate jumped to 6.2%, the highest on official state record.
Manufacturing buckled as China’s manufacturing-purchasing-managers index fell to 35.7 in February from 50 in January, the lowest reading recorded since the state began this survey in 2004. For industries, the government-imposed shutdown strained performance as production, new orders, delivery times, and staffing levels all fell at record rates.
The challenge was captured appropriately by Scott Settersten, CFO of the US-based cosmetics company Ulta Beauty: “The situation is dynamic, and it’s very difficult to predict or quantify the impact of any potential disruption to our supply chain, changes in consumer demand, or any other actions that may become necessary as events unfold”.
With China’s temporary paralysis, global supply chains have choked. Companies everywhere find themselves in a tussle to find diverse sources of supplies for every product one can think of, not in the least toilet paper and personal protective equipment. The situation is dire and, evidently, it’s not just in China.
Speaking to the Financial Times, S&P Global’s Jun Hong Park, stated that, “If the supply chain outages persist, this could disrupt Samsung and LG Electronics.” Why might that be the case? Simply because the different components of many of the world’s electronic gadgets come from several different countries. So, while China may be recovering, the world needs South Korea, Japan and Vietnam to be on the same part of the disease curve, otherwise tighter transport restrictions, production closures and shortage of essential raw materials — electronic chips and phone screen panels — will not be able to leave or reach the factories that need them.
Take Apple. iPhone camera parts and Apple Watch screens are made by LG, a South Korean company operating largely in Vietnam but mostly assembled in China. In Europe for instance, after the German border to Poland was closed, trucks lined up for 65km near Berlin.
Ethan Harris, head of global economic research at Bank of America stated that, “In terms of the impact on global production, the shutdown outside of China will likely become bigger than the impact from China.” The ripple effects of delayed supplies and the uncertainty in the supply chain have far-reaching implications.
Factories on lockdown
It is for this reason that Lasher Tools, with the added advantage of sourcing more than 90% of its inputs locally, has benefited. Its four factories are back to life and engines revving.
In a recent article by Business Day, Lasher, a local manufacturer and supplier of hand tools, landed a multi-million-rand deal in the wake of shortages in China’s factories. For the 90-year-old Lasher Tools, “[The coronavirus] has re-ignited our factories,” according to the marketing manager Albert Louw. Lasher’s opportunity is indicative of how manufacturing base can serve the continent, and beyond.
Today, the SA government is investigating how the production of hand sanitiser, gloves, face masks and test kits may be bolstered in the country — and from where needed, imported components may be sourced, according to a report by Fin24. This is a good path to pursue, now and in the future.
Of course, this might all collapse as SA factories enter lockdown.
In Europe, 69% of trade is cross-border, and 59% in Asia; in Africa, that number is a paltry 17%% — the lowest intra-regional trade in the world. And yet, combined, the 55-member states of the AU have a total population of 1.3-billion, projected to reach 2.5-billion in the next two decades, and a combined GDP of more than $3.4-trillion. Encouraging internal consumption and intra-regional trade will be essential to trigger a manufacturing boom that will establish the continent as a manufacturing hub for its inhabitants.
The contribution of manufacturing to GDP for Sub-Saharan countries is 11%, lower than the global average (15%) and even worse when compared to East Asia & Pacific (23%).”
To cater for its burgeoning and largely poor population, African leaders needs to focus heavily on manufacturing, and the African Continental Free Trade Agreement (AfCFTA) is the perfect vehicle to develop a regional manufacturing base. While China will fight to reclaim the world, Africa, through the AfCFTA must fight for Africa.
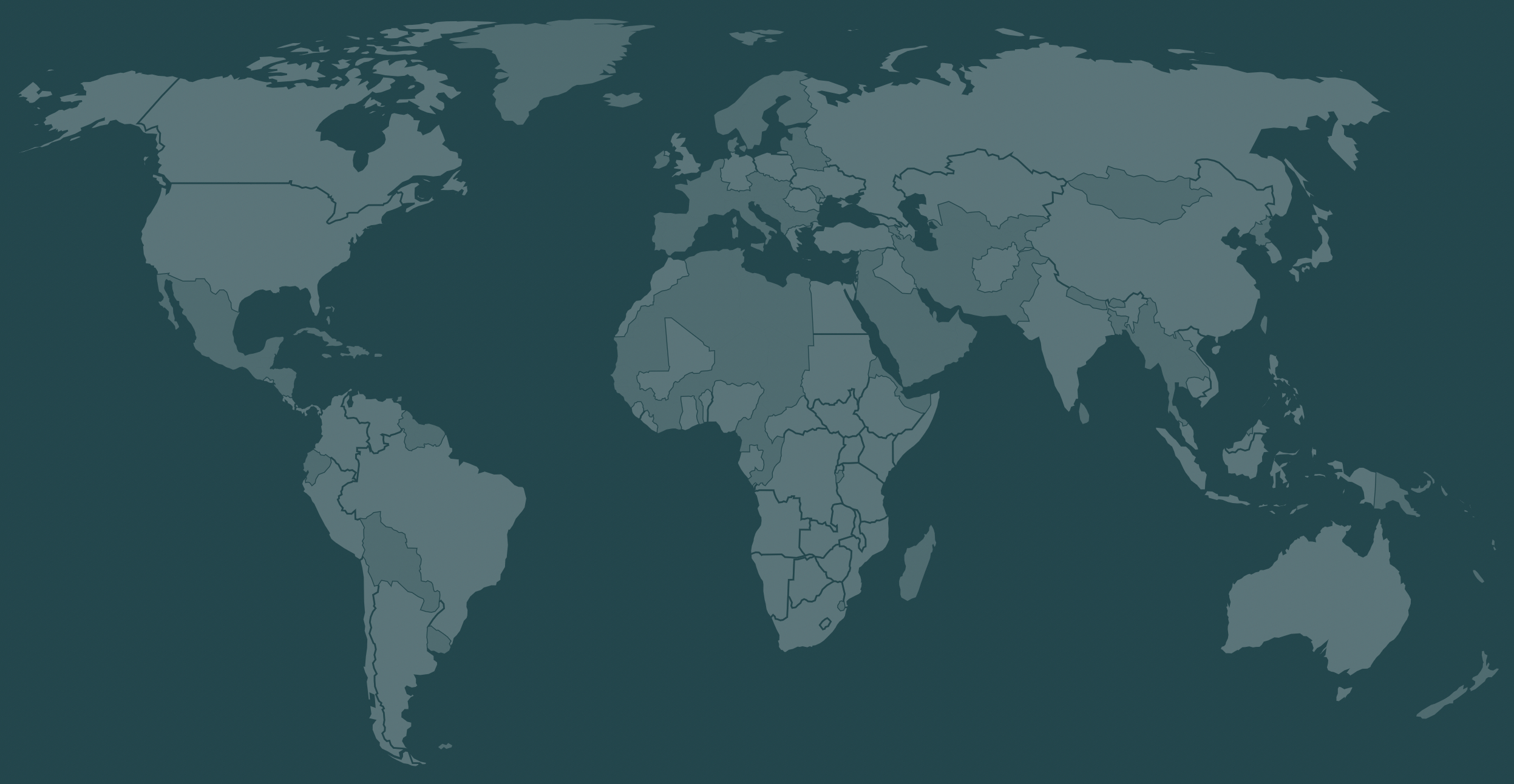
Africa needs to do more internally. Developing a regional value chain will comprise bigger industries obtaining their supplies from smaller industries across Africa’s borders. Simultaneously, less-industrialised countries can profit from linking to regional value chains to build capacity and secure higher incomes from value-added industrial production. By reducing trade costs and facilitating investment, AfCFTA makes the development of regional value chains more desirable and easier.
Thinking economically is not to underplay the realities of COVID-19, certainly not. But, we do need to think beyond it as well. Africa houses three of the five countries with the highest number of extreme poor in the world: Nigeria, the Democratic Republic of the Congo (DRC) and Ethiopia. One in three Africans live below the global poverty line — a total population that represents 70% of the world’s poorest people.
How African countries tackle the pandemic will have major implications for not just physical survival but also the 6,000 Africans who fall into poverty every day, in spite of COVID-19. Africa’s leaders cannot afford to take their eye off the ball of creating economic prosperity for its citizens because when this is over, as it would be, the economic and financial carnage to contend with would be ginormous.
Asia offers some lessons in this regard. Japan survived at least three great restorations over the last 150 years, each one faster than and markedly different from the one before. For example, in August 1945, the atomic bomb dropping on Hiroshima and Nagasaki led to the demise of more than 100,000 people. Yet, four months after this devastation, Mazda had resumed production and was not the only firm to do so.
Underlying Japan’s recovery and added growth was a combination of governance and a relentless attitude. Even though the American occupation saw to the dismantling of Japan’s industrial complex, many Japanese companies adapted to produce products for their domestic household markets instead. Japan rebuilt its economy so fast that by the start of the Korean War it became the key suppliers of US matériel, which saw manufacturing soar by 50% between 1950 and 1951.
Estimates place US expenditure on Japanese companies, including Mitsubishi and Sumitomo, for the duration of the war at about $3.5bn (or U$33bn in 2019 terms). Not long after the Japanese industrial complex kicked off again, its shipyards were in operation and, within a decade, Japan had overtaken Britain as the world’s biggest shipbuilders. If there was ever an inspiring story, it might be that.
Japan’s lessons for Africa are many — not in the least to act fast. Their success was testament to the importance of seeing opportunity in crisis and creating a laser-like focus on development needs, from jobs to infrastructure, and of a readiness to make key sacrifices to ensure progress.
The pandemic teaches us that an anti-fragile and robust supplier management system that takes into account sub-tier dependencies and proximity is a prerequisite for today’s supply chain, and that is a lesson African leaders must not forget in drawing up, negotiating and framing the inner working of Africa as an industrial base under AfCFTA.
Africa’s 420-million young people, aged 15—35, already face an uncertain future and how this turns out depends on the decisions that are made today. Japan’s precision, ability to see opportunity where all seemed lost, and fortitude are timely lessons for Africa’s leaders.
Certainly, more questions need to be asked about straightening kinks in African regional integration, economic links, and policy strategies most conducive to ensuring that African countries reap their share of global economic gains, but as presidents Olusegun Obasanjo, Ellen Johnson Sirleaf and Kgalema Motlanthe have said, now is the time to act locally and think globally.
This article was originally published in BusinessDay.